A gasket is the epitome of “small but strong,” and while they go unnoticed in almost all of their applications, they are also one of the main reasons machinery is able to perform at peak efficiency. Varying in size, shape, and material, gaskets are compressed between two joining components to create a seal, while compensating for materials unable to interlock on their own due to imperfect surfaces. Gaskets can be as simple as the rubber O-ring in a hose nozzle, as prevalent as the head gasket in automobile engines, or as vital as intermediaries in fuel or coolant systems for aeronautics.
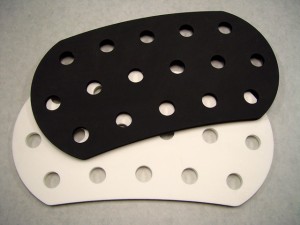
These products can be manufactured out of a multitude of materials, depending on their application. One such material is foam, and given their production capabilities and materials, Foam Factory, Inc. is the right choice for gasket manufacturing, on a small or large scale.
Foam gaskets are most frequently made of closed-cell foam, given its ability to resist the transmission of air and fluid. Because of their light weights and durability, cross-linked polyethylene (XLPE) and neoprene are most frequently used in applications where closed-cell foam gaskets are desired, as well as polyethylene. Polyethylene foam roll is also sometimes utilized for its flexibility. The greatest benefit of a foam gasket though, is its cost-effectiveness. Compared to traditional rubbers, metals, and silicone, foam rubber can perform at a much lower price than other products.
Neoprene is the most popular foam gasket material because of the utility its molecular structure provides. While soft and flexible enough to be compressed, this closed-cell material remains strong, resistant to Ozone, sunlight, oxidation, many chemicals and petroleum derivatives, as well as breakdown by water and air. This versatility makes it an excellent product for creating a low-pressure gasket seal in applications where frequent replacement is difficult. Examples of neoprene gaskets include seals in central air conditioning units, air filter gaskets, fishing livewells, and applications involving gasoline and oil.
XLPE has similar properties and capabilities to neoprene, but is especially useful for applications where thicker gaskets are required. XLPE is extremely fine-celled, nontoxic, and contains no CFCs, HCFCs, or hydrocarbon blowing agents, making it an excellent material for applications where there are concerns about maintaining the continuity of the substance passing through the gasket. An additional benefit of XLPE is the material’s availability in multiple colors: red, blue, green, purple, yellow, black, and white. For situations where an organization has machinery requiring many different gaskets of similar shape and size, gaskets can be color coded, greatly reducing the chances of accidentally using the wrong gasket and damaging machinery. If one component always receives green gaskets, the similarly sized red gaskets will never be used, a mistake that could potentially be made using identical colors.
Polyethylene is often used as thermal gaskets in construction for assisting in the insulation of homes. One of its most important jobs is as a sill plate gasket between a structure’s foundation and the sill plate section of lumber that wall studs are placed on. These thin sheets form a seal between the wood and concrete that can’t be made independently because of their imperfect, rigid surfaces. This insulation gasket prevents air, moisture, and even insects from entering the structure. Polyethylene is also used as expansion joint filler in masonry between concrete slabs, reducing the amount of joint fill that must be added while still maintaining a degree of flexibility. Polyethylene is excellent in low temperature and low-pressure gasket applications as well.
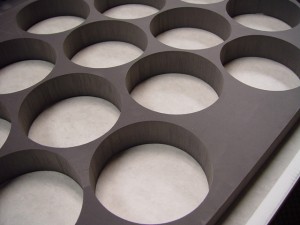
With our fleet of cutting and stamping machines, Foam Factory is able to efficiently produce both short-run and bulk projects for any use. The waterjet cutter is programmed on a computer to make precision cuts to materials using a .005 inch stream of water at 60,000 psi. Crisp angles and smooth contours can be cut with the waterjet to create custom gaskets for a perfect seal.
For bulk orders, the die cutter is able to produce hundreds of thousands of products quickly, using a stamping process that can produce many pieces in a single pressing, depending on size. Dies, also called plates, are inset with thin metal blades so that when foam is compressed over them by the press, the corresponding shapes are sliced out like a cookie cutter. These pressings are optimized to produce the maximum number of products in each stamping, with the cutting table large enough to accommodate multiple dies at once. For example, 30 O-rings, measuring a sizable 6 inches in diameter, can be produced in one stamping. After removing the cut pieces, a new sheet of foam is placed over the dies and the process repeats, taking just minutes for turnaround time.
Whether you need a couple gaskets for a weekend project or 100,000 pieces to outfit a new product your company is introducing, Foam Factory will earn your “seal” of approval by producing exactly what you need quickly and economically.
WOW!
Fast service,good prices and the cushions fit perfect!!
Great job!
Thanks
Jack Weisner